Цифровая сертификация
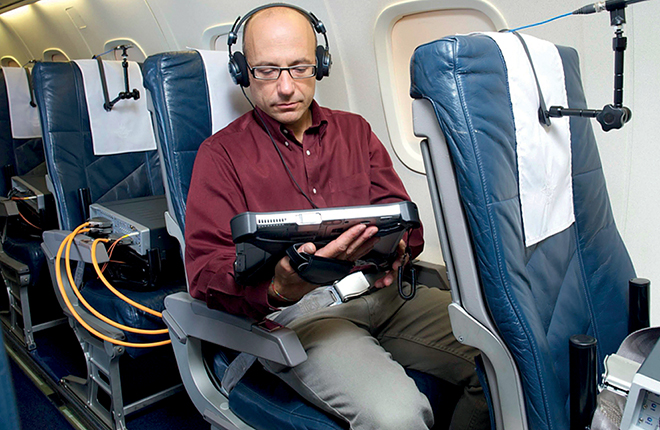
Вызовы при разработке и сертификации авиационной техники
Количество авиационных перевозок на протяжении последних десяти лет постоянно растет. Если в 2009 году из-за последствий глобального финансово-экономического кризиса объемы пассажирских перевозок сократились на 1,2%, то уже в 2010 году этот показатель увеличился на 8% и не сокращался на протяжении последующих лет. В 2018 году пассажирские перевозки увеличились на 6,5%, и в 2019 году этот показатель, по оценке Международной организации гражданской авиации (ИКАО), составит не менее 6%.
В 2018 году авиакомпании по всему миру выполнили 38 миллионов рейсов, перевезли 4,3 миллиарда человек и 58 миллионов тонн грузов. По прогнозам экспертов, к 2035 году объем авиаперевозок пассажиров и грузов увеличится по меньшей мере в два раза. Об этом в январе 2019 года заявил президент ИКАО Олумуива Бенард Алиу. При этом около 70% роста авиаперевозок придется на уже существующую маршрутную сеть. Авиакомпании учитывают этот рост и планируют наращивать авиационный парк.
В то же время ужесточаются требования к шумности и экологичности новых летательных аппаратов. Действующие Парижские соглашения в области сокращения объемов вредных выбросов требуют в 2 раза снизить объемы выбросов парниковых газов авиацией к 2050 году. С одной стороны, растущий спрос на новые летательные аппараты стимулирует авиапроизводителей создавать новые самолеты и вертолеты, но с другой — ужесточение экологических норм и требований к потреблению топлива значительно усложняет и удорожает разработку авиационной техники.
В сложившихся жестких условиях цена ошибки высока как никогда. Так, задержка программы пассажирского лайнера Airbus A350 на два года из-за необходимости перепроектирования отдельных узлов самолета привела к увеличению стоимости проекта почти на 3 миллиарда евро. Серьезные финансовые потери из-за переноса сроков и конструкторских ошибок понес европейский концерн Airbus и в проекте разработки военно-транспортного самолета A400M. Стоимость программы разработки японского регионального самолета MRJ компанией Mitsubishi Aircraft из-за задержек на 6 лет выросла чуть больше, чем на 3 миллиарда долларов.
Чтобы добиваться успеха разработчикам авиационной техники приходится переосмысливать подходы к проектированию и испытаниям летательных аппаратов, прибегать к использованию новых решений и материалов, а также повышать сложность своих изделий. Это увеличивает сроки наземных и летных испытаний авиационной техники и ее сертификации в соответствии с новыми стандартами. Как результат, возрастает стоимость сертификационных испытаний.
По словам исполнительного директора по коммерческим самолетам компании Rockwell Collins Кента Статлера, сертификация самолетных систем сегодня порой обходится существенно дороже их разработки, при том что прежде из каждого доллара, израсходованного на проект, 75 центов шли непосредственно на разработку, а оставшиеся 25 центов – на сертификацию. В компании Siemens PLM Software уверены, что применение современных цифровых технологий позволяет сэкономить и ускорить разработку авиационной техники за счет автоматизации заметной доли расчетов и сертификационных испытаний.
Дигитализация на всех этапах
Традиционный подход к созданию современной авиационной техники, включая ее бортовое оборудование и программное обеспечение, начинается с концептуального проектирования и заканчивается сертификацией. В случае с пассажирскими самолетами стоимость всех мероприятий по сертификации может превышать 100 миллионов долларов, причем именно процесс сертификации нередко приводит к задержкам в разработке авиационной техники и росту стоимости программы в целом. Нередко этап сертификационных испытаний определяет, будет проект прибыльным или убыточным.
Основной целью сертификации является подтверждение того, что летательный аппарат и его системы полностью соответствуют нормам летной годности. В ходе сертификации проект проходит два этапа: валидацию и верификацию. Первый подразумевает проверку правильности и полноты предъявляемых к нему требований. Тогда как второй призван подтвердить, что разработанное воздушное судно полностью удовлетворяет предъявляемым к нему требованиям, прошедшим валидацию.
Применение интегрированных решений Siemens PLM Software существенно ускоряет процесс верификации и, как следствие, сертификацию. Например, с помощью решения Teamcenter Verification Management становится возможным интегрировать управление требованиями, конфигурациями и изменениями, данными расчетов и испытаний, и обеспечить гарантию прямой и обратной прослеживаемости выполнения всех требований и характеристик. В результате можно избежать ошибок, связанных с человеческим фактором и необходимостью синхронизации результатов между разными отделами и соисполнителями. Благодаря Teamcenter все актуальные данные в любой момент времени доступны всем участникам процесса верификации.
Решения Siemens PLM Software помогают перенести процесс верификации на более ранние этапы разработки, обеспечивая большой потенциал для сокращения бюджетов и сроков программы. Технологии Siemens PLM Software позволяют создавать верифицированные модели летательных аппаратов, их агрегатов, узлов и систем, и проводить их виртуальные испытания. Для типовых авиационных систем и компонентов решения предлагают уже существующие библиотеки настроенных моделей, благодаря чему становится возможным выполнение достоверных расчетов и отказ от части натурных испытаний. Их результаты заменяются результатами виртуальных испытаний.
Благодаря высокому качеству верифицированных 1D-моделей Simcenter Amesim в ряде случаев результаты моделирования расходятся с результатами реальных испытаний не более чем на 1%. Использование других решений из портфеля Simcenter, объединяющего технологии для 1D- и 3D-моделирования, а также натурных испытаний, позволяет проводить достоверные расчеты для режимов, которые трудно или даже невозможно проверить в рамках физических испытаний. Речь, в частности, идет о расчете границ флаттера или моделировании различных аварийных ситуаций. Еще одним преимуществом виртуальных испытаний является возможность частично заменить, а в некоторых случаях и полностью отказаться от части дорогостоящих испытаний в аэродинамической трубе или на специализированных стендах типа "железная птица".
Сокращение сроков сертификации становится возможным благодаря более точному планированию натурных испытаний. Так, верифицированные модели, полученные с помощью решений Simcenter, позволяют заранее определять места наилучшего размещения датчиков и режимы испытаний отдельных узлов, агрегатов и летательных аппаратов в сборе. Кроме того, с помощью технологий Simcenter Testing можно значительно автоматизировать процесс испытаний – проводить автоматические расчеты и анализ данных эксперимента непосредственно в темпе испытаний. В этом случае снижается риск влияния человеческого фактора и во многом отпадает необходимость "ручной" обработки огромного массива данных.
Решения Siemens PLM Software позволяют построить процесс верификации с учетом разработки нескольких конфигураций летательных аппаратов. Например, разные конфигурации самолета могут включать агрегаты разных производителей, часть летных испытаний которых можно провести в лаборатории или вообще заменить расчетом, значительно сократив объем летных испытаний и затраты на их подготовку и проведение. Отчеты по результатам таких испытаний или расчетов служат основанием для подтверждения требований, проверяемых сертифицирующими органами.
Всеобъемлющий цифровой двойник
Технологии Siemens PLM Software позволяют предприятиям реализовать концепцию "цифровых двойников". Компания-разработчик интегрирует все цифровые процессы в едином формате и обеспечивает всем вовлеченным в проект сотрудникам доступ, стремясь создать всеобъемлющий цифровой двойник. Всеобъемлющий цифровой двойник – это взаимосвязанная комбинация цифровых двойников разрабатываемого продукта, производства и изделия в эксплуатации. Он соединяет требования с производством и эксплуатацией для непрерывного улучшения продукта и его производства, сокращает цикл разработки, повышает эффективность и гибкую адаптивность под меняющиеся рыночные требования, позволяет воплощать больше инновационных идей в жизнь.
Цифровой двойник продукта подразумевает создание виртуальной полностью верифицированной модели самолета или вертолета, проведение практически полного спектра инженерного анализа (путем расчетов и/или испытаний), проверки соответствия требованиям и виртуальной доводки. Анализ включает, проверку аэродинамических характеристик, характеристик прочности и усталостной долговечности конструкции, тепловых режимов, режимов обледенения, вибрационных и акустических колебаний. Такая цифровая модель с высокой точностью соответствует реальному образцу, уточняется по результатам наземных или летных испытаний и позволяет учитывать все изменения, происходящие с реальным самолетом.
Цифровой двойник производства – гарантия своевременного выхода на сертификацию в рамках определенных сроков и бюджета с требуемым качеством. Она используется на самых ранних этапах планирования производства будущего изделия, например, для имитационного моделирования производства посредством решения Tecnomatix Plant Simulation. Благодаря ему становится возможным прогнозирование трудностей при организации производства, а также оптимизация производственных процессов и взаимодействия с поставщиками. Это позволяет добиться минимизации ошибок, которые могут быть допущены при реальном производстве. Наконец, цифровые двойники позволяют отработать и техпроцесс. И все это задолго до запуска реального производства.
После выполнения четырех шагов – виртуального проектирования, виртуального производства, запуска реального производства и создания летательного аппарата – цифровой двойник позволяет учитывать все особенности эксплуатации самолета или вертолета. Поступающие на этом этапе жизненного цикла данные могут быть использованы для доработки и модернизации изделия, а также заложить основу для разработки перспективных изделий. По оценкам экспертов Siemens PLM Software, внедрение цифровых технологий в проекте пассажирского самолета вместимостью 150-170 человек позволяет снизить ежегодные расходы на разработку на 290-300 миллионов евро, в том числе, и за счет ускорения процесса сертификации. Так, Федеральное управление гражданской авиации США позволяет заменять натурные испытания некоторых изменений конструкции летательных аппаратов аэродинамическими расчетами, которые подтверждают, что такая модификация не приведет к нарушению требований летной эксплуатации и снижению безопасности самолета.
Как это работает на практике
Решения Siemens PLM Software успешно используют разработчики авиационной техники по всему миру. В некоторых случаях в процессе сертификации разработчики использовали результаты виртуальных испытаний, выборочно подтвержденные реальными проверками. Европейский авиастроительный концерн Airbus при разработке топливозаправочной штанги самолета-заправщика Airbus A330MRTT прибегал к виртуальным испытаниям. В этом проекте достоверные результаты были получены еще на этапе моделирования флаттера и позднее подтверждены натурными испытаниями.
Еще одним успешным примером использования цифрового подхода к проектированию, испытаниям и сертификации является разработка лайнера Airbus A380. Французская компания Safran Landing Systems, занимавшаяся созданием шасси этого самолета, использовала решение Simcenter Amesim. A380 был введен в эксплуатацию с передней стойкой шасси, разработанной и настроенной полностью по 1D-модели, созданной в Simcenter Amesim. Результаты виртуальных испытаний шасси полностью подтвердились натурными. При этом разработчику удалось ускорить реализацию проекта за счет точного планирования испытаний и прогнозируемости эксперимента.
Airbus использовал Simcenter Amesim для создания цифровых двойников самолета A380, его топливной системы и двигателей, которые затем прошли испытания на виртуальном стенде. С помощью такого виртуального стенда специалисты смогли спрогнозировать и оценить эффекты пульсации давления в топливной системе. По оценке разработчиков, цифровой подход позволил уменьшить время, необходимое на доработку и доводку топливной системы, почти на 2 года. При традиционном подходе, подразумевающем полный цикл натурных испытаний, потребовалось бы больше времени и средств на создание и настройку стенда и проверку работы систем самолета.
Историями успешного использования решений Siemens PLM Software могут поделиться многие разработчики, в числе которых Boeing, Airbus, Airbus Helicopters, Kaman Aerospace, Honda Aircraft, Embraer и другие. Полученный при решении конкретных задач опыт подтверждает, что решения Siemens PLM Software позволяют оптимизировать, ускорить и удешевить процесс сертификации летательных аппаратов, обычно занимающий значительную часть в бюджете проекта.